В.И. Панов, д-р техн. наук, ОАО «Уралмашзавод» (Екатеринбург)
О показательном сварочном производстве Уралмашзавода сказано много, работы его ведущих специалистов и рабочих отмечены высокими государственными наградами. Приведем лишь отдельные моменты истории, малоизвестные широкому читателю.
Сварочное производство Уралмаша пережило несколько этапов.
Первый этап создания сварочного производства (1928–1933 гг.) начался одновременно со строительством завода. Специалисты, проектировавшие завод, предложили начать его строительство с сооружения цеха металлоконструкций (ЦМК). Эту идею горячо поддержал начальник строительства Александр Петрович Банников. 15 июля 1928 г. состоялась торжественная закладка первого камня в основание фундамента первого цеха — цеха металлоконструкций.
В изготовлении металлоконструкций дуговая сварка в те времена почти не применялась. Сварные конструкции были большой редкостью. Металлоконструкции выполнялись с помощью клепки (рис. 1). Возле ЦМК размещался огромный плац для производства клепальных работ. Это был тяжелый малопроизводительный труд. К тому же клепальные молотки издавали такой шум, что рабочие быстро теряли слух. Клепальщиков называли «глухарями».
Также 15 июля 1928 г. Управление строительством Уралмашиностроя организовало отдел по проектированию, производству и возведению металлических сооружений.Его возглавил молодой инженер Григорий Петрович Михайлов.
Первый производственный цех будущего завода вошел в строй 15 июля 1929 г. на три месяца раньше намеченного срока: группа проектировщиков во главе с Г.П. Михайловым заранее подготовила чертежи конструкций каркасов цехов.
Г.П. Михайлов родился 1 января 1899 г. в Елабуге. Первоначальное образование он получил в реальном училище (1916 г.), а в 1924 г. окончил Московский институт инженеров путей сообщения. Молодой специалист прекрасно знал, что такое металлоконструкции. В 1927–1928 гг. Г.П. Михайлов руководил строительством нового мартеновского цеха Пермского пушечного завода, и он начал применять сварку при изготовлении металлоконструкций.
Надо учесть, что Г.П. Михайлов работал на заводе, где его горный управитель Н.Г. Славянов создал дуговую сварку плавлением металлическим электродом. Под его руководством было отремонтировано более 1600 наименований различных деталей особо ответственного назначения: гребные валы пароходов, сосуды давления, лафеты пушек и многое другое. Восстановленные конструкции успешно эксплуатировали долгое время. Поэтому можно предположить, что Г.П. Михайлова захватили разработки Н.Н. Славянова, и он видел в них будущее развитие производства металлоконструкций. (Читайте статью «История сварки»).
Но его позицию многие не разделяли, сварные конструкции особого энтузиазма не вызывали. Поэтому первоначально с помощью сварки изготовляли хозяйственный инвентарь, емкости, лестницы, ограждения и др. Постепенно задачи усложнялись. В 1930 г. были спроектированы и изготовлены сварные междуэтажные перекрытия. У современного инженера первая сварная ферма, предназначенная для первого механического цеха, вызвала бы улыбку. Она представляла собой смесь элементов, являющихся традиционными составными частями такого рода конструкций (пояса, раскосы и др.), и большого числа дополнительно установленных различных уголков, косынок, накладок. По мере совершенствования ферм число дополнительных крепежных деталей уменьшалось. Таким образом, сварные металлоконструкции стали первой продукцией Уралмашзавода, точнее Уралмашиностроя.
Сооружение будущего гиганта тяжелого машиностроения потребовало большого количества металлоконструкций, которые надо было изготовлять на месте. Однако в то время практически отсутствовала отечественная и зарубежная литература по этому вопросу. Г.П. Михайлов сыграл выдающуюся роль в коренном изменении взглядов на сварку. По его инициативе были организованы курсы по обучению сварщиков и специализации инженерно-технических работников (проектировщиков, конструкторов и технологов). Для проведения занятий были приглашены крупнейшие отечественные специалисты сварочного дела проф. В.П. Вологдин, проф. К.К. Хренов и др. Первый выпуск курсов в 1930 г. насчитывал 39 человек, а в 1932 г. — уже 50 человек. В 1932 г. были созданы курсы для инженеров-сварщиков (рис. 2).
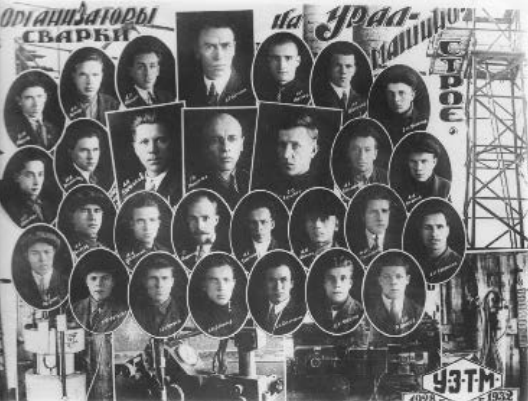
Рис.2. Выпуск первых технологов-сварщиков. Третий ряд (в квадратных рамках) слева направо: А.А. Кирилов, Г.П. Михайлов, В.Е. Волынко
Такая подготовительная работа немедленно дала результаты. Для строящегося завода были изготовлены мачты для прожекторов высотой 24 м, дымовые трубы высотой до 40 м. Была выполнена сварка газопровода протяженностью 3 км. К качеству сварки подобных сооружений предъявляют исключительно высокие требования. Проектирование таких конструкций иначе как технической дерзостью не назовешь. А в то время обоснованных норм и технических условий к сварным конструкциям еще не было. Многое определялось интуицией, грамотностью и смелостью проектанта. Еще до официального пуска завода ЦМК Уралмашиностроя изготовил 27 тыс. т металлоконструкций для строящегося завода тяжелого машиностроения и для других гигантов отечественной промышленности: Магнитогорского металлургического комбината, Первоуральского Новотрубного завода и других заводов.
Помимо Г.П. Михайлова, большая роль в организации базы по проектированию и изготовлению металлоконструкций на Уралмашзаводе принадлежит конструктору, а затем старшему мастеру Д.Г. Ницбергу (будущему коммерческому директору Уралмашзавода), конструктору Д.И. Беренову (впоследствии главному инженеру Уралмашзавода), технологам В.Н. Соловьеву, А.А. Кириллову, А.А. Урбанскому и др.
К середине 1930-х годов Уралмашзавод стал признанным лидером по изготовлению сварных конструкций крупных размеров.
На третьем Всесоюзном автогенном съезде (Москва, март 1931 г.) немецкий специалист Шмуклер демонстрировал как крупнейшее достижение сварную подкрановую балку длиной 5 м. Выступивший на следующий день в качестве докладчика от строящегося завода Г.П. Михайлов рассказал об опыте изготовления сварной конструкции подкрановых балок для кранов грузоподъемностью 50 т и длиной пролета 10 м.
Инженер необычайно широкого кругозора, Михайлов известен фундаментальными разработками способов расчетов конструкций экскаваторного оборудования, канатных дорог. Он также занимался проектированием железных дорог и железнодорожных мостов. Г.П. Михайлов был человеком невероятной работоспособности. Не отрываясь от Уралмашзавода, в 1931 г. он по совместительству работает помощником заведующего кафедрой металлоконструкций, а в 1932–1934 гг. — заведующим кафедрой строительной механики и металлоконструкций. В 1933 г. заканчивает еще один вуз — Уральский металлургический институт. Через несколько лет он организовал одну из первых отечественных кафедр сварочного производства, которую он возглавлял (с перерывами) до своей кончины в 1958 г.
По инициативе Михайлова в 1932 г. была создана исследовательская группа, которую возглавил Алексей Алексеевич Кириллов. В дальнейшем она переросла в многопрофильную сварочную лабораторию. Когда в 1962 г. был создан научно-исследовательский подотдел отдела главного сварщика Уралмашзавода, она стала основой для создания лабораторий для исследования сварочных процессов, наплавки, механизированных способов сварки, электрошлаковой сварки, проблем металловедения и электротехники.
И снова нельзя не отметить роль Г.П. Михайлова, но на этот раз как крупнейшего ученого-электротехника. Он создает новое научное направление — сварку трехфазной дугой. По сравнению с однофазной сваркой производительность при этом способе возрастает в 1,5–2 раза, а экономия электроэнергии составляет 25–30%.
Основы сварки переменным током разработал академик В.Ф. Мицкевич в 1903–1905 гг. В «Сварочном вестнике» (1927 г.) и в журнале «Электричество» (1932 г.) сообщалось о больших затруднениях, связанных с трехфазной сваркой. Так, инженер И. Зак писал, что схемы, предложенные Гольслэгом в США, Шмидтом в Германии, Бетено во Франции, Клинкгамером в Голландии теоретически неправильны и практически неприемлемы. Другие авторы считали, что основная причина, задерживающая внедрение этого способа сварки, — отсутствие специальных сварочных трансформаторов. Эту проблему решил проф. Н.С. Сиунов, будущий ректор УПИ им. С.М. Кирова. Для питания сварочным током был разработан специальный трансформатор.
Под руководством Г.П. Михайлова был проведен огромный комплекс работ. Он включал исследование трехфазной электрической дуги и ее воздействие на процесс сварки; исследование различных способов сварки трехфазной дугой; разработку сварочных материалов, оснастки и оборудования для трехфазной сварки и другие принципиально важные вопросы.
Ко второму этапу создания сварочного производства относится предвоенный период 1933–1941 гг., когда сварку стали применять при изготовлении машин и оборудования, она становится процессом, заменившим клепку. С использованием сварки стали производить мостовые и козловые краны, вагранки и другие ответственные конструкции, например, станины фанерных прессов. Тогда специальная фанера широко применялась в производстве боевых самолетов.
Описывая два периода становления сварочного производства Уралмашзавода, нельзя не отметить Владимира Евгеньевича Волынко (1900–?). Судя по архивным данным, это была исключительно неординарная личность с совершенно необычной судьбой. Первоначально он учился в Екатеринбурге в горном институте, созданном по прямому указанию Николая II. Во время гражданской войны сначала воюет на стороне белых, затем переходит на сторону красных. В 1920 г. студент третьего курса Московской горной академии уезжает на практику на золотоносные прииски и в вуз не возвращается. На различных приисках он занимает достаточно ответственные должности, а в 1923 г. резко меняет свою специальность: становится электросварщиком. В 1925–1926 гг. В.Е. Волынко выполняет восстановительные работы конструкций особо ответственного назначения на Надеждинском металлургическом заводе (ныне город Серов). Вызывает удивление талант, ум и дерзость этого молодого человека. Даже в наши дни найдется не много специалистов, способных решать задачи на таком высоком инженерном уровне. Свой опыт Волынко обобщил в цикле лекций для специалистов сварочного производства «Дуговая сварка в ремонтном деле». По оценке крупнейшего авторитета того времени А.Н. Огиевского — это было первое в мире подобное издание.
С 12 января 1930 г. Владимир Евгеньевич — работник Уралмашинстроя в должности инструктора электросварки ЦМК. Затем он работал инженером-проектировщиком, старшим инженером сварки, заведовал курсами по подготовке сварщиков для Уралмашзавода. Среди наиболее ярких работ Волынко, выполненных совместно с А.А. Урбанским и другими электросварщиками, — сварка бака вместимостью 700 м3 водонапорной башни Уралмашзавода, пожалуй, одного из самых значимых памятников эпохи конструктивизма, широко известного под названием «Белая башня» (рис. 3). Подобная работа была сделана в Чикаго, но вместимость бака была много меньше.
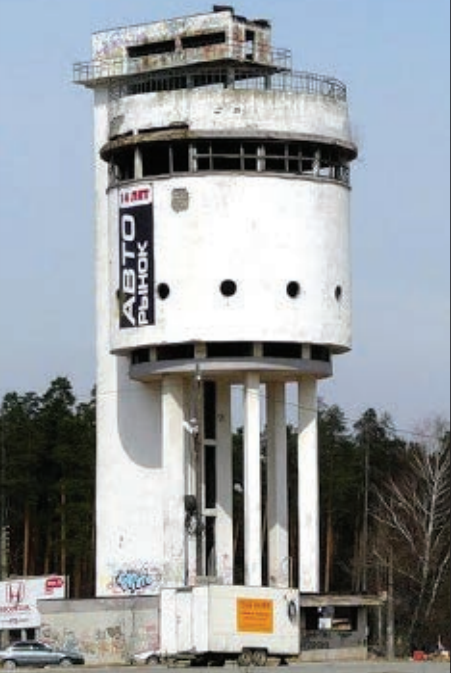
Рис.3. Памятник эпохи советского конструктивизма — водонапорная башня архитектора М.В. Рейшер (1929 г.).
О признании уникальности работ В.Е. Волынко свидетельствуют многочисленные факты. Он принял участие в работе 1-го Всесоюзного автогенного съезда специалистов сварочного производства. В.Е. Волынко неоднократно избирали членом Уральского областного бюро инженеров и научных работников сварочного дела. К сожалению, В.Е. Волынко повторил печальную судьбу многих людей того времени.
После ликвидации Российской ассоциации пролетарских писателей (РАППП) в Свердловск был сослан Леопольд Авербах, племянник Я.М. Свердлова, дальний родственник видного партийного деятеля В. Бонч-Бруевича. Он был назначен редактором уралмашевской многотиражной газеты, а затем избран секретарем парткома завода. Кстати, именно Авербах послужил для М.А. Булгакова прообразом Воланда в романе «Мастер и Маргарита». Авербах сожалел, что на Уралмашзаводе до сих пор не было публичных политических дел. Случай подвернулся. Из-за элементарной безграмотности и безответственности рабочих — вчерашних крестьян, сгорел кузнечный цех, в те годы крупнейший в Европе. В ходе процесса, на котором Авербах был главным обвинителем, обвинения были предъявлены 10 крупнейшим заводским специалистам. Четверо из них были приговорены к расстрелу. В.Е. Волынко присудили 10 лет. Его дальнейшая судьба неизвестна. В 1956 г. он письменно обратился в отдел кадров Уралмашзавода с просьбой выслать трудовую книжку. На этом следы этого талантливого специалиста потерялись.
Сварщики Уралмашзавода в 1930-е годы приняли участие в реализации одного из самых грандиозных проектов современности.
Эта история началась на Первом съезде Советов СССР, состоявшемся в 1922 г., где С.М. Киров предложил «воздвигнуть новый дворец рабочих и трудящихся крестьян» на месте «дворцов банкиров, помещиков и царей». Но тогда эта идея «еще не вызрела». О ней вспомнили в 1924 г., когда возник вопрос об увековечении памяти В.И. Ленина. «Нужно построить грандиозное здание, которое должно стать одновременно памятником В.И. Ленину, Коминтерну и образованию Союза ССР», — таково было решение руководства Всесоюзной Коммунистической партии (большевиков).
В середине 1930-х годов Уралмашзавод приступил к изготовлению сварных конструкций для Дворца Советов. Для них отечественными металлургами была создана сталь марки ДС («Дворец Советов»). По тем временам она считалась особо прочной. Технологам и рабочим Уралмашзавода нужно было освоить принципиально новую марку стали и в короткие сроки наладить производство сварных конструкций.
Одной из особенностей этой стали было наличие в ней меди. Этот элемент, помимо повышения коррозионной стойкости металла, вызывает красноломкость, то есть при ее сварке возникает повышенная опасность образования горячих трещин, что было недопустимо. Требовалось разработать приемы и режимы заготовительных операций, сборки и сварки особо ответственных конструкций. С 1940 г. начался монтаж каркаса сварных конструкций сооружения, причем он выполнялся очень быстрыми темпами.
Начавшаяся Великая Отечественная война внесла свои коррективы. Уже в сентябре — октябре 1941 г. из подготовленных для монтажных работ сварных металлоконструкций были изготовлены противотанковые ежи для обороны Москвы. В этой работе принимали участие и уралмашевцы.
Уралмашзаводу была поставлена задача в кратчайшие сроки освоить производство броневой стали и обеспечить ее выпуск в требуемом объеме. Задача казалась неразрешимой, так как южные металлургические заводы находились на оккупированной фашистами территории. Поэтому заводскими специалистами было предложено в качестве основы использовать сталь «ДС», которая осталась на Уралмаше. Затем настала очередь собранного каркаса Дворца Съездов. После оккупации Донбасса стальные конструкции Дворца Советов были использованы для сооружения мостов вновь построенных железнодорожных магистралей. По ним перевозили уголь, добытый в северных районах, в центральные районы страны.
Полученный опыт позволил Уралмашзаводу в очень короткие сроки уже в послевоенные годы, в период восстановления разрушенного войной хозяйства, освоить производство особо ответственных конструкций индивидуального тяжелого машиностроения из аналогичной марки стали 10ХСНД, в состав которой также входит медь.
В конце прошлого века при сооружении Храма Христа Спасителя выяснилось, что грандиозный фундамент Дворца Советов сохранился, поэтому цикл работ, связанный с его изготовлением, был коротким. Возможно, в фундаменте храма сохранились изделия первого поколения уралмашевских сварщиков — уникальные металлоконструкции.
Еще студентами мы знали, что на Уралмашзаводе работает легенда отечественной и мировой ремонтной сварки Вячеслав Алексеевич Батманов (рис. 4) и что самым молодым среди уралмашевских начальников цехов является Николай Рыжков — начальник сварочного цеха № 31 (бывший ЦМК), одного из самых сложных цехов. Тогда мы, конечно, не предполагали, что симпатичный долговязый парень будет последним Председателем Совета министров СССР.
Впервые В.А. Батманова я встретил в один из жарких летних месяцев 1957 г., во время прохождения практических занятий на Уралмашзаводе. Он был человек небольшого роста, но коренастый, сразу бросалась в глаза его скромная одежда. Тогда, в свои 67 лет, Батманов вел на заводе активную деятельность и занимался защитой дипломного проекта. Его выдающаяся по тем временам работа была о холодной сварке чугуна, фактически он один из первых предложил технологию такой сварки и активно внедрял ее на производстве. (Читайте статью «Сварка чугуна»).
После завершения института я начал свою трудовой путь в ОГС (отделе, который занимался сваркой) Уралмашзавода. С Батмановым часто не приходилось видеться, но когда происходили эти редкие встречи, он меня приветствовал не иначе, как«товарищ Панов». Тогда, впрочем, все так друг к другу обращались. Моим непосредственным руководителем В.А.Батманов, который заведовал лабораторией сварки, стал в 65 г., мы работали плечом к плечу вплоть до его смерти в 69 г.
Это был выдающийся профессионал и человек во всех смыслах этого слова. Очень эрудированный, он получил основательное образование в домашних условиях, часто читал стихи русских классиков. Его отец А.Н. Батманов — родом из Питера, арестант Петропавловской крепости, который, собственно, в Екатеринбург был сослан. В последствии он стал известным деятелем в культурной жизни Екатеринбурга, был одним из отцов-основателей Уральского общества любителей естествознания (УОЛЕ), которое было долгое время центром общественно краеведческого движения.
Изучать сварку Батманов начал задолго до Первой мировой войны в Петербурге, осваивая профессию сварщика на Путиловском заводе (сегодня Кировский) и на судостроительном заводе «Северная верфь».
Поступил в Императорский электротехнический институт имени Александра Третьего. В 1916 г. окончил военное училище, приобрел офицерское звание — прапорщик. В 1918 г. В.А. Батманов примкнул к Белому движению, однако Гражданскую войну 1917-1922 он закончил в рядах Красной армии. Служил в радиотехнических войсках.
Секреты сварочного искусства В.А. Батманов продолжал постигать на Черноморском судостроительном заводе, затем на Верх-Исетском металлургическом заводе (Свердловск).
В энциклопедии по сварке, увидевшей свет в Соединенных Штатах Америки в 1930 г., говорится, что в то время Батманову не было равных в ремонтной сварке особо ответственных толстостенных и крупногабаритных металлоконструкций. Он был специалистом с мировым именем, имел тесные связи с American Welding Society — AWS, расположенной в Маями.
То, что было сделано Батмановым, по сегодняшний день вызывает восхищение, потому что даже с современными технологиями и возможностями проделанные им работы трудно повторить:
- 1926 г. — ремонт цилиндра (чугун) реверсивной паровой машины (Надеждинское металлургическое предприятие). Была удалена и впоследствии заварена трещина длиной 2,5 м;
- с 1935 г. В.А. Батманов — работник Уралмашзавода, его трудовая книжка исписана благодарностями за многочисленные, успешно выполненные ремонтные работы;
- 1936 г. — восстановление цапфы валка диаметром 800 мм прокатного стана;
- 1939 г. — ремонт высочайшего качества цилиндра парореверсивной машины в сжатые сроки.
Он был награжден значком «Отличник соц.соревнования» (за подписью народного комиссара танковой отрасли Малышева), значком «Ветерана московского Метростроя» за разработку технологического процесса ремонтной сварки тюбингов, а в 1966 г. он получил почетную медаль «За трудовую доблесть».
Как музейный экспонат, у меня на сохранении находится рабочий блокнот Батманова со списком производственных задач и выполненных работ. Работоспособность, и как сейчас модного говорить, стрессоустойчивость была огромной и сил хватало даже в преклонном возрасте. Даже в 72 лет рабочая смена Батманова длилась более двенадцати часов, темпы были стахановские.
В книжках В.А. Батманова по ремонтной сварке собран весь богатый многолетний опыт. Они переведены на десятки иностранных языков и актуальны в сегодняшнее время. Сам В.А. Батманов был превосходным сварщиком. До войны электроды для заварки дефектов больших размеров готовили по следующей технологии: стержни диаметром 10–12 мм обвязывали шнуром из асбеста, который крепили к металлическому прутку обычной проволокой, затем погружали в водный щелочной раствор силикатов калия и натрия и сушили. Какой геркулесовой силой надо было обладать, чтобы варить в течение смены и держать в руках такой вес. Сварочный ток был большой 1000–1100 А. Размеры сварочной ванны и масса расплавленного металла были огромные. Нужен был действительно большой талант, чтобы в таких условиях не просто работать, а еще и обеспечивать высокие визуальные и прочностные характеристики сварочных швов. (Читайте статью «Как производят сварочные электроды»).
Когда Батманов занимался ремонтно-восстановительными работами крупногабаритных узлов, рядом всегда находились различные ферросплавами, которые время от временем добавлялись в присадочный материал для легирования стали и придания швам необходимых свойств. Он не просто как попало сыпал порошкообразные добавки, этому предшествовал предварительный скрупулёзный теоретический расчет.
В начале 1941 г. вышла из строя станина пресса, на котором изготавливали штамповкой заготовки валков для прокатки броневых сталей, самолетных пропеллеров, узлов танков и самоходок. Надо было обладать большим мужеством и глубокими познаниями материаловедения в области поведения металла тяжелонагруженного оборудования, чтобы в таких непростых обстоятельствах (в случае провала могло грозить тюремное заключение) предложить абсолютно инновационную технологию — вварку пакета пластин в жесткий контур. Много лет спустя материаловеды назовут такую технологию «батмановским» швом. Когда же вварка была успешно проведена в сжатые сроки, Вячеслава Алексеевича спросили, чем его отблагодарить. Он попросил тарелку супа.
Источник: журнал «Сварщик»