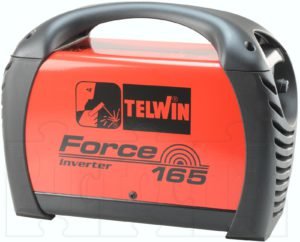
В данной статье немного приоткроем завесу над буднями обычного сервисного центра по ремонту сварочной техники. Сегодня вашему вниманию представляем ремонт сварочного инвертора Telwin Force 165. Возможно, ознакомившись с предоставленной информацией, вы сможете устранить некоторые неисправности своими руками. И помните, не беритесь за ремонт, если не уверены в своих действиях, в результате, это всегда обходится дорого.
Как ни банально это звучит, ремонт начинается с разборки аппарата. Для начала снимается ручка, которая зафиксирована на 4 винтах. Затем откручиваются 2 винта, расположенные на пластмассовой части (держат переднюю и заднюю панель) и 2 винта, которыми зафиксирован корпус по бокам). Также не забудьте снять ручку регулятора тока, потянув ее на себя, потому что она не позволит передней панели инвертора отделиться от общего корпуса.
Диагностика начинается с поверхностного осмотра платы. Нужно внимательно посмотреть, нет ли перегоревших дорожек, поврежденных элементов и тому подобного. При беглом осмотре сразу видно, что вышел из строя зарядный резистор, который отвечает за плавный заряд конденсаторов.
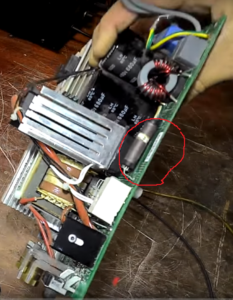
Без него будет большой удар в сеть. То, что сгорел зарядный конденсатор говорит о 3 вещах:
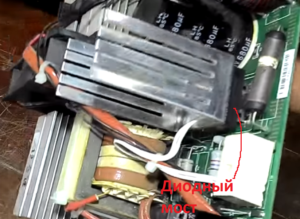
- Пробиты электролитические конденсаторы;
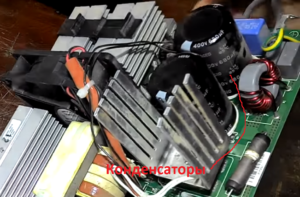
- Силовые ключи – IGBT транзисторы.
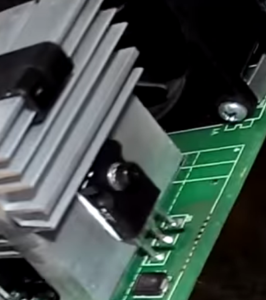
Приступаем к прозвонке
Начать прозвонку лучше с выходных клемм, таким образом проверяется годность выходного диодного моста.
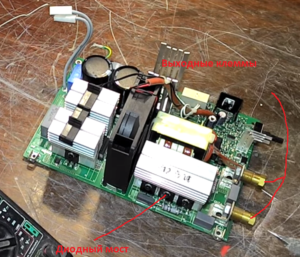
Затем проверяются
- входной мост с обратной стороны платы;
- диодный мост на предмет КЗ;
- конденсаторы по высокой стороне;
- силовые транзисторы IGBT нужно замерять меду стоком и истоком, то есть между коллектором и эмиттером.
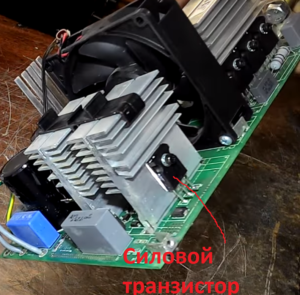
В данном конкретном случае ремонта Telwin Force 165 вышли из строя именно транзисторы.
Обычно, при выгорании транзисторов выгорают и драйверы. В таком случае транзисторы нужно демонтировать. После демонтажа транзисторов нужно проверить исправность драйверов. Для этого находят сопротивления 15 Ом и звонят их в режиме прозвонки тестера. Если они целы, большая вероятность, что драйвер годный. Если же эти резисторы в обрыве, тогда придется полностью проверить драйвер. Рядом расположены диоды и транзисторы, их проверяют на пробой.
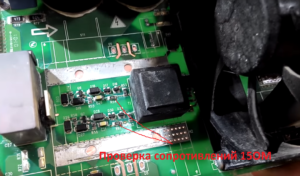
Перед включением нужно убедиться, что у нас по высокому нет замыкания (что замыкание было действительно в транзисторах). Проверяем на конденсаторах.
Топология данного инвертора, Telwin 165, это косой полумост. Выходной трансформатор включен между транзисторами. Почему так называется, косой полумост? Транзисторы включены как бы наискось. В другом косом плече моста стоят разрядные диоды. Их нужно прозвонить заранее, потому что при пробое транзисторов очень часто эти диоды тоже пробивает.
Проверяют также супрессоры – снабберы транзисторов. Они вылетают редко.
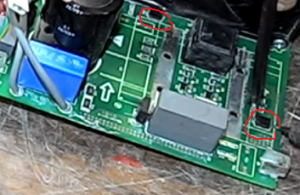
Если КЗ нет, нужно подать питание и осциллографом посмотреть, какой сигнал приходит на транзисторы. Многие ремонтники смотрят на форму сигналов на затворах, но мы рекомендуем от эмиттера до затвора впаивать конденсатор 220 -1000 пФ. Тем самым имитируется емкость затвора и нагружается цепочка драйвера. Таким образом, весь драйвер выходного транзистора думает, что он работает на затвор транзистора. Осциллограмма будет примерно такой, как при работе с реальным транзистором. Без нагрузки все может хорошо показывать, под нагрузкой – мы увидим, какая будет форма.
Перед подключением питания в обязательном порядке понадобится стоваттная лампочка с двумя проводами. Если вы не опытный ремонтник, вам нужно обрезать дорожку на плате. Дело в том, что вы можете не заметить замкнутый трансформатор, битый снаббер, диоды и т.д. Разрез питающей дорожки вас спасет от дорогостоящего выхода всей силы из строя.
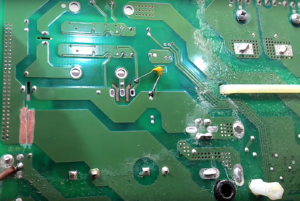
После любой манипуляции, когда вы включили питание, а потом выключили его, нужно на лампочку разрядить конденсаторы. Напряжение на них смертельное, 310В, может быть даже летальный исход.
В процессе наладки, между двумя разрезанными дорожками впаивается лампочка, которая ограничивает ток, идущий через выходную часть. И даже если где-нибудь что-то будет не так (занижена частота, пробиты трансформаторы, выход и т.д.), лампочка просто загорится в полный накал, а все остальное останется целым.
В Telwin Force 165 схема построена следующим образом: как таковая отсутствует дежурка, но … через резистор от сетевого напряжения (310В) заряжаются конденсаторы, которые дают подпитку ШИМу и он короткими импульсами пытается запустить силовую часть. В момент запуска силовой части отвод из силового трансформатора через диод и кренку начинает питать всю схему. Вся схема «заводится» — в этот момент щелкает реле и включается вентилятор. Таким образом производится запуск инвертора, т.е он работает на самоподпитке (не от дежурки). Если вы включили инвертор и щелкнуло реле, завращался вентилятор – это значит, что сила «завелась».
В конкретной рассматриваемой плате при подаче питания на указанных на фото выводах между эмиттером и затвором должны быть короткие «пачки» импульсов – попытки запуска — примерно раз в одну секунду.
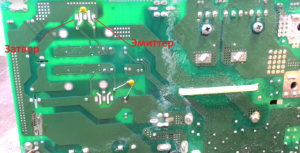
Для проверки нужно подпаять минусовой щуп осциллографа на эмиттер.
Важный момент! Напряжение, которое вы подаете, должно быть развязано от сети гальванически, чтобы осциллограф и все остальные приборы, которые вы подключаете, не попали попали под фазу (включая человека, который ремонтирует инвертор).
Другой щуп осциллографа ставится на затвор и подается питание.
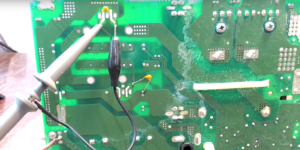
На экране осциллографа должны появится серия запускающих импульсов. Значит, драйвер, ТГР, и управляющий ТГРом транзистор – все в рабочем состоянии.
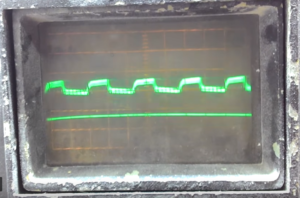
Затем, отключается питание, разряжаются конденсаторы на лампочку и производится переключение на другое плечо.
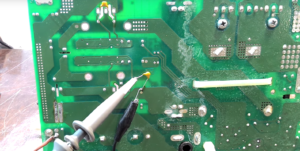
Проверяются импульсы на другом плече. С помощью осциллографа вы можете измерить размах посчитать их длительность.
Запаиваем весь конечный каскад и пробуем его запустить, потому что все работает в штатном режиме, о чем свидетельствует описанная проверка.
При установке новых силовых IGBT –транзисторов все поверхности алюминиевых радиаторов, к которым они будут прилегать, должны быть идеально чистыми: очищены от любых загрязнений и промыты спиртом.
Проведите пальцем по радиатору в месте установки транзисторов: не должно быть вкраплений, отверстия под резьбу без заусениц и не должны возвышаться (когда откручивают винт, бывает как-бы «вытаскивают» резьбу из алюминия – получается бугор).
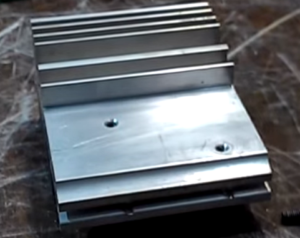
Нужно убедиться, что на IGBT-транзисторах нет вкраплений, потому что любая песчинка сделает зазор между транзистором и радиатором, соответственно, функция теплоотвода не будет выполняться в полной мере.
Пасту КПТ-8 (Кремнийоргани́ческая Па́ста Теплопрово́дная) ГОСТ 19783-74, используемую для улучшения теплообмена между мощными электронными компонентами и радиатором, нужно наносить на транзистор исключительно из тюбика. Не нужно выковыривать пасту лопатками из банок.
Пасту нужно мазать как можно меньшим слоем и только на металлическую часть. При затяжке транзистора она должна едва выйти из-под корпуса. Толстый же слой приводит к деформации транзистора.
Радиаторы с транзисторами обратно устанавливаются на плату и запаиваются. В технологический разрез дорожки платы, о котором говорилось ранее, впаивается лампочка, после чего подается питание. Должно щелкнуть реле и включиться вентилятор, это значит, что силовая часть запустилась. Если лампочка не горит, это говорит о том, что все работает нормально и ток покоя в норме.
Нужно проверить выход. На выходных клеммах инвертора должно появиться напряжение. Проводите все работы очень аккуратно, потому что схема в момент проверки находится под высоким напряжением 310В по постоянному току!
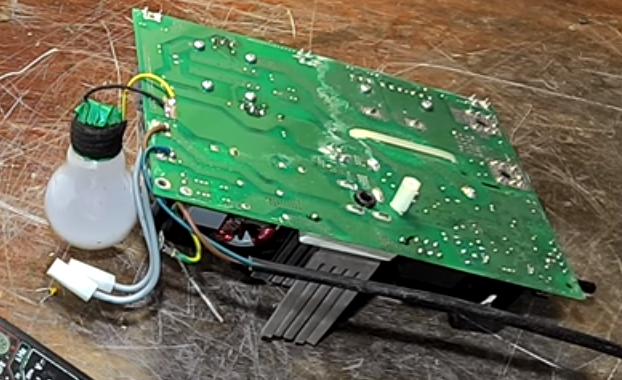
К выходным клеммам подключается небольшая лампочка 40 Вт и если все в норме, она должна загореться – силовая часть в рабочем состоянии.
Далее плата промывается изопропиловым спиртом от паяльного флюса, восстанавливается «разорванная» дорожка и нагружается на реостат (проверяется выходной ток).
Регулятор тока выводится на минимум и подключается реостат. Ставятся щупы и снимается напряжение холостого хода. Подключается нагрузка и регулируется ток ручкой инвертора. В данном конкретном случае ремонта ток не регулировался, т.е. был постоянно на максимальном своем значении. Если бы в качестве нагрузки был бы подключен не реостат, а реальный сварочный электрод, при первом же касании о металл этим электродом, вся силовая часть сгорела бы снова, так как инвертор постоянно работает на максимальной своей мощности! Оказывается, изначальная проблема, приведшая к поломке, заключалась в отсутствии регулировки тока. Это говорит о том, что неисправность находится где-то в задающем генераторе. Следствие выбитой силы уже было отремонтировано, а причину – нужно искать.
За регулировку тока отвечает трансформатор, через который проходит первичная обмотка силового трансформатора. Нужно проверить целостность вторичной обмотки этого регулировочного трансформатора. Операционник LM324 проводит сравнение между установленным положением ручки регулятора тока в одном плече и полученными данными с указанного на фото транса в другом плече.
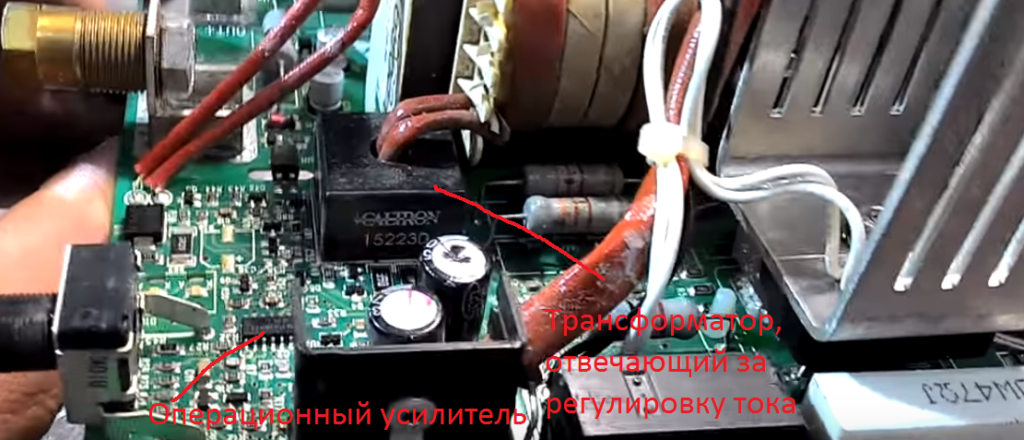
Результаты, полученные операционником, подаются на микросхему ШИМ (задающий генератор работы всей силовой части) и от длительности его импульсов зависит выходной ток. Длительность же импульсов задается операционной микросхемой на основании полученных данных между установленной ручкой и тем, что пришло с трансформатора. В данном случае ремонта данная схема не работает. Нужно устанавливать причину.
Заменой микросхемы компаратора LM324 проблема была решена, а ремонт инвертора завершен. Дальнейшее испытание на реостате показали, что аппарат полностью исправен, а ручка регулировки тока работает, как и положено.
Источник: Powerful Electronics