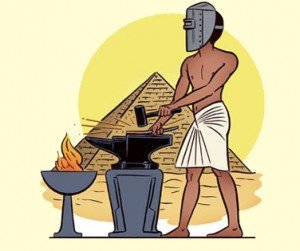
Истоки . .
Историческое развитие сварки можно проследить с древнейших времен. Самые ранние артефакты относятся к бронзовой эпохе. Небольшие золотые короба, хранящиеся в Ирландском национальном музее, были получены фактически сваркой давлением, которая, как известно, не требует нагрева, и производится путем пластичной деформации при комнатной температуре. Предполагается, что эти короба были изготовлены более 2 тыс. лет назад.
В железном веке египтяне и жители восточной части Средиземноморья научились сваривать куски железа вместе. Многие инструменты, которые были найдены, сделаны в период около 1000 г. до н.э.
В средние века своего рассвета достигло кузнечное искусство и многие изделия, которые появились в ту пору, были сварены ковкой, пока в 19-ом веке не изобрели сварку, какой мы ее знаем сегодня.
1800 г
Считается, что ацетилен был открыт англичанином Эдмундом Дэвисом. А вот первым получить дуговой разряд удалось другому английскому химику, одному из основателей электрохимии, почетному члену множества научных организаций, в том числе Петербургской Академии наук, сэру Гемфри Дэви. Дуговой электроразряд был получен им между двумя графитовыми стержнями, которые были подключены к полюсам электрической батареи, составленной из 2 тыс. гальванических элементов.
Начиная с середины 19 века изобретен электрогенератор, и набирает популярность освещение при помощи дугового разряда. А уже к концу 19 века появилась газовая сварка и резка, дуговая сварка угольным и стальным стержнем, сварка электросопротивлением.
1880 г
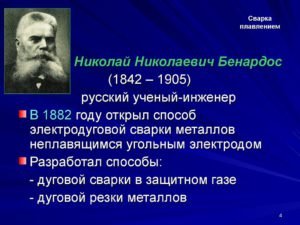
Огюст де Меритан, проводя в 1881 г исследования в лаборатории Кебот во Франции, применил тепло электродуги для сплавления свинцовых пластин аккумуляторных батарей . В то время его учеником был молодой русский ученый Николай Николаевич Бенардос, который работал с де Меританом в лаборатории во Франции и стал фактически отцом сварки. Патент на способ дуговой электросварки «Электрогефест» присвоен Николаю Бенардосу и Станиславу Ольшевскому. Британский патент выдан в 1885 г и американский – в 1887г. Также Бернадосом разработан первый электрододержатель и прочее. И хотя сварка графитовым стержнем была ограничена в возможностях, ею уже в те времена можно было варить железо и свинец. Способ стал широко внедряться в конце 1890 г – начале 1900г.
1890 г
Н.Г. Славянов представил свой вариант идеи металлопереноса через дугу (через стальной стержень), а также приспособил данный метод для литья в литейную форму и получил Российский патент на способ электрической отливки стали.
В то же время в 1890 году основатель компании «General Electric» Ч.А. Коффин из Детройта запатентовал в США точно такой же процесс электродуговой сварки стальным стержнем, который плавился под силой дуги, с последующим металлопереносом в сварочную ванну и кристаллизацией сварного шва.
1900 г
Приблизительно в 1900 г А.П. Штроменгер (Strohmenger), имя которого не известно на постсоветском пространстве, представил в Великобритании первый стальной электрод с тонким покрытием из глины или извести, которое стабилизировало дугу.
А вот электрод с флюсующей обмазкой изобрел швед Оскар Челльберг, стоявший у истоков компании ЕСАБ. Работы над созданием обмазки велись с 1907-1914 г.г. Штучные электроды были изготовлены протяжкой и порезкой цельнометаллической проволоки на прутки с последующим погружением в растворы карбонатов и силикатов. После высыхания они были готовы к реализации.
В то же время британский инженер Элиу Томсон придумал контактную сварку.
В 1903 году немец Гольдшмидт (буквально «золотых дел мастер») изобрел термитную сварку, с помощью которой соединили железнодорожные рельсы.
В течение этого времени также развивалась газовая сварка и резка. Производство кислорода, а позже и сжижение воздуха, наряду с изобретением газовой горелки этому способствовало . До 1900 года предпринимались попытки сварки в кислородно-водородном пламени, причем смесь находилась в одном баллоне. Обратный удар мог привести к мощному взрыву, поэтому химик Сент-Клер Девилем решил разделить газы и смешивать их в горелке. Процесс стал безопасней, но на выходе Сент-Клер получил низкотемпературный факел 2200 градусов. И только в 1901 г. французы Эдмон Фуше и Шарль Пикар изобрели ацетилено-кислородную горелку, чертежи и характеристики которой существенно не поменялась и до сегодня.
Первая мировая война спровоцировала милитаризацию заводов и для сварки наступил «золотой век». Начали массово выпускаться сварочные машины и электроды к ним.
1920 г- настоящее время
В 20-е годы разработаны разные виды сварочных электродов, составлены рецепты новых флюсующих обмазок, ведутся дискуссии по методологии их производства. Введение маркировки металлов требовало создания классификации обмазок и используемых стальных стержней электродов. Требовалось создавать более надежные сварочные швы.
В 20-е годы было основательно исследовано влияние защитных газов на сварочный процесс, так как О2 и N2 воздуха при контакте с жидким металлом сварного шва вызывала пористость и горячеломкость. В зону сварки подавались различные газы, затем вся тщательно анализировалось.
Американский химик Ирвинг Ленгмюр провел опытную работу с водородом в качестве защитной сварочной атмосферы. Он поставил два электрода рядом с друг другом, сначала из графита, позже из вольфрама. Между ними поджигалась вольтовая дуга в атмосфере водорода и наблюдалось активное расщепление молекул водорода на атомы. Температура диссоциированного пламени составляла ~ 3700° С, что достаточно для сварки, а высокая активность водорода обеспечивала прекрасную защиту металла шва от вреда, причиняемого О2 и N2 воздуха. Процесс получил название атомно-водородной сварки, но большого распространения не получил и применяется преимущественно для инструментальных сталей.
Подобную работу провели также американцы H.M. Hobart и P.K. Devers, только они работали с аргоном и гелием. Итогом эмпирических изысканий данных господ стал патент на электродуговую сварку в среде газа, которую можно считать первым шагом в деле создания современного инверторного аппарата аргонодуговой сварки, появившегося, правда, гораздо позднее. Запатентованый процесс идеально подходил для сварки Мg, Al, а также стали, легированной Cr и был доведен до совершенства в 1941 году, Технология получила название дуговой сварки неплавящимся вольфрамовым электродом в среде инертных газов. Сегодня она применяется, как на производстве, так и в быту. Чаще всего используются аппараты АрДС. Было в том числе разработано оборудование для работы в среде инертных/активных газов плавящимся электродом, который представляет собой сварочную проволоку, проходящую через подающее устройство к соплу горелки по гибкому шлангу.
1928 г
В 1928 году в Советском Союзе Д.А. Дульчевским изобретена автоматическая сварка под флюсом. Развитие же процесса началось в конце 30-х годов благодаря усилиям научных работников института электросварки АН УССР под началом академика Е.О. Патона, что сыграло большую роль в деле танкостроения, выпуска орудий и авиационных бомб в годы ВОВ. Сварка под флюсом нашла широкое применение во всех отраслях народного хозяйства. Это эффективный способ получения прочных швов при хорошем КПД.
В США процесс автоматической сварки получил название «сварки погруженной дугой в порошке». Его запатентовал в 1930 г. некто Robinoff, а затем продал его Linde Air Products Company. В 1938 году сварка под флюсом активно использовалась на верфях и артиллерийских заводах.
В 1930 г. был разработан любопытный процесс Stud сварки для Нью-йоркской военно-морской верфи. С помощью Stud осуществлялось крепление деревянных настилов над металлической поверхностью. Stud сварка стала востребована в судостроительной и строительной отраслях.
В 1949 году в институте им.Патона в Киеве появилась на свет электрошлаковая сварка, которая сняла ограничения со сварки крупногабаритных изделий. Теперь можно варить любые толщины! Процесс был представлен мировой общественности на Брюссельской Всемирной выставке в Бельгии в 1958 году
В 1953 г. К. В. Любавский и Н. М. Новожилов изобрели весьма экономичный способ сварки плавяшимся электродом в среде СО2. Новый способ получил мировое признание, так как он позволял работать на обычном оборудование для сварки в инертном газе.
В 1957 г. комиссариатом по атомной энергии Франции был раскрыт процесс электронно-лучевой сварки, который нашел применение в автомобилестроительной и авиационной отраслях.
В 1957 году Роберт Ф. Гейдж изобрел процесс плазменной дуговой сварки. Температура в плазмы около 30 000°С, в отличие от электрической дуги, температура которой не более 5000–7000°С.
1960 г
Начинается использование газовых смесей, заключающееся в добавлении к инертному газу небольшого количества кислорода. В целом, использование смесей для различных сталей дает положительный результат. Внедряется сварка в режиме импульсного тока.
Вскоре после изобретения советскими учеными популярного способа полуавтоматической сварки в углекислоте (СО2) было придумано взять плавящийся электрод-проволоку с флюсовым сердечником. Флюсующий порошок при плавлении давал дополнительную газовую защиту изнутри , снаружи применялась защита углекислотой. В 1959 году была придумана проволока-электрод, которая не требовала внешней газовой защиты. Сейчас она известна под названием «самозащитная флюсовая проволока», приобретается она чаще всего для случаев, когда невозможно использовать газ. С этой проволокой нет необходимости таскать туда-сюда баллон с газом.
И на закуску…
Сварка трением придумана в Советском Союзе. Здесь работает принцип превращения механической энергии в тепловую за счет сил трения, возникающих при соединении с определенным усилием сжатия двух деталей.
Лазерная сварка – инновационный сварочный процесс. Лазер был первоначально разработан в Bell Telephone Laboratories в качестве устройства связи. Но благодаря способности концентрировать огромное количество энергии в небольшом объеме, он оказался еще и мощным источником тепла, что используется сегодня для высокоэффективной сварки и резки металла.